Hydraulic System Overview
🛠 What is a Hydraulic System?
A hydraulic system is a power transmission system that utilizes incompressible fluid, typically hydraulic oil, to transfer energy through components such as pumps, valves, actuators, and piping. It works on Pascal’s Law, which states that pressure exerted anywhere in a confined fluid is transmitted equally in all directions.
Hydraulic systems are widely used in industries requiring high force and precision control. Examples include heavy machinery (excavators, bulldozers), industrial presses, aircraft control systems, and marine steering mechanisms. These systems are valued for their efficiency, compactness, and reliability, particularly in applications demanding rapid response and consistent force output.
🔍 Core Components of a Hydraulic System
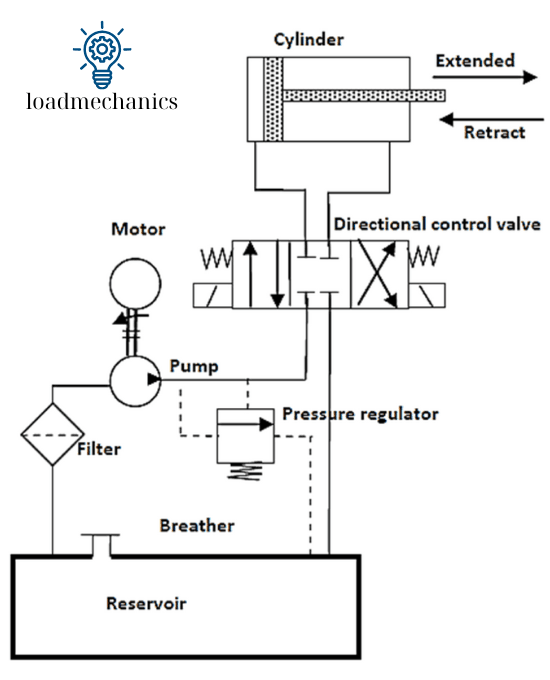
Here are the fundamental components that form the backbone of every hydraulic system:
1. Hydraulic Pump
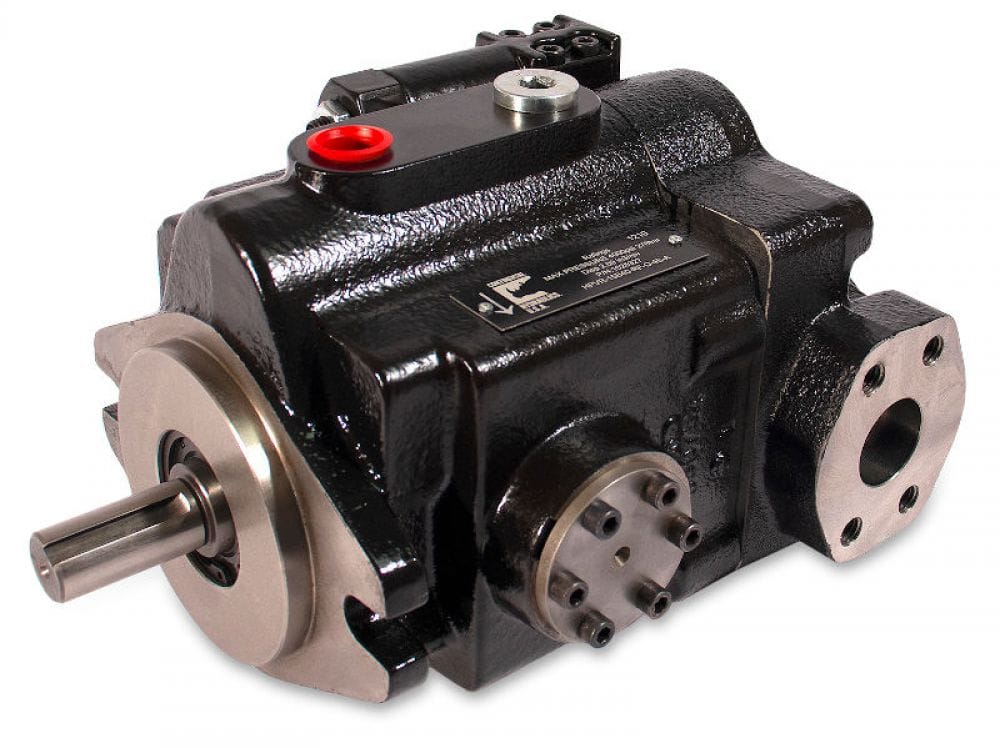
The hydraulic pump is the heart of the system. It converts mechanical energy from a prime mover (like an electric motor or engine) into hydraulic energy. There are several types:
- Gear Pumps: Simple and cost-effective
- Vane Pumps: Quieter with moderate pressure capability
- Piston Pumps: High efficiency and pressure, suitable for industrial applications
A well-designed pump ensures steady flow and is selected based on system pressure, flow requirements, and duty cycle.
2. Hydraulic Valves
Valves control the direction, pressure, and flow rate of the hydraulic fluid. Common types include:
- Directional control valves
- Pressure relief valves
- Flow control valves
→ Learn more: Hydraulic Control Valve
→ See comparison: Pressure Relief Valve vs Reducing Valve
3. Hydraulic Cylinders & Actuators
Hydraulic actuators convert hydraulic energy into mechanical motion. Types include:
- Cylinders (Linear Actuators): Deliver straight-line motion (single or double acting)
- Hydraulic Motors (Rotary Actuators): Deliver rotary motion with high torque
These are used for lifting, clamping, pushing, or rotating parts in machines.
4. Reservoir (Tank)
The reservoir stores hydraulic fluid, provides heat dissipation, and helps separate air and contaminants. It must be adequately sized to accommodate thermal expansion and system refill needs. A well-ventilated reservoir with baffles can improve fluid settling and reduce turbulence.
5. Filters
Clean hydraulic fluid is critical. Filters are placed at suction, pressure, and return lines to trap particulates and maintain fluid cleanliness, typically rated in microns. Monitoring filter clogging indicators and replacing elements regularly help prevent system damage.
6. Hydraulic Fluid
Hydraulic fluid performs four functions:
- Power transmission
- Lubrication of components
- Heat dissipation
- Contamination removal
Choosing the right fluid involves considering viscosity, temperature range, and compatibility with materials. Synthetic fluids, biodegradable oils, and fire-resistant types are selected based on specific application requirements..
How a Hydraulic System Works
Understanding the operational workflow of a hydraulic system is essential for designing, troubleshooting, and optimizing its performance. Below is a detailed step-by-step explanation of how a typical closed-loop hydraulic system functions:
1. Energy Input and Pump Operation
The cycle begins with the prime mover (typically an electric motor or diesel engine) supplying mechanical power to the hydraulic pump. The pump draws hydraulic fluid from the reservoir and converts mechanical energy into hydraulic energy by pressurizing the fluid. In positive-displacement pumps (gear, vane, piston), this is achieved by trapping a fixed amount of fluid and forcing it into the hydraulic circuit.
- Inlet stroke: Fluid is drawn into the pump chamber under atmospheric or reservoir pressure.
- Discharge stroke: The pump pressurizes the fluid and pushes it through the system.
2. Flow Control and Direction Management
Pressurized fluid exits the pump and travels to a directional control valve (DCV). This valve determines the path of fluid flow based on operator input or automated signals. The DCV directs the fluid to one side of a hydraulic actuator (e.g., a cylinder or motor) while simultaneously allowing return flow from the opposite side to be routed back to the reservoir.
- Solenoid-actuated or pilot-operated valves can be used for remote and automated control.
- Valve spools are shifted to change actuator direction (extend, retract, rotate CW/CCW).
3. Pressure Regulation and Overload Protection
As fluid flows, pressure control valves ensure that pressure levels remain within safe operating limits. These include:
- Relief valves: Open to divert excess fluid to the tank if system pressure exceeds a preset limit.
- Sequence valves: Prioritize actuator operation in a specific sequence.
- Pressure reducing valves: Maintain a reduced pressure in sub-circuits.
This ensures equipment safety, avoids energy loss, and maintains predictable actuator behavior.
4. Actuation and Mechanical Work
Hydraulic fluid reaches the actuator, where its pressure energy is transformed into mechanical work:
- In cylinders, fluid pushes against the piston face, generating linear force.
- In hydraulic motors, fluid flow drives the rotor to produce rotary motion and torque.
Force output (F) in a cylinder is calculated using: F = P × A, where P is pressure (Pa) and A is piston area (m²).
The speed of motion depends on flow rate (Q): v = Q / A for linear actuators and ω = Q / D for rotary actuators, where D = displacement volume.
5. Return Flow and Heat Dissipation
After performing its work, the fluid exits the actuator and returns to the reservoir through a return line, passing through:
- Check valves to prevent reverse flow
- Return filters to remove contaminants
- Heat exchangers to dissipate accumulated heat
Temperature control is critical, as excessive heat reduces fluid viscosity, damages seals, and accelerates wear. Target operating temperature is typically around 40–60°C.
Applications of Hydraulic Systems
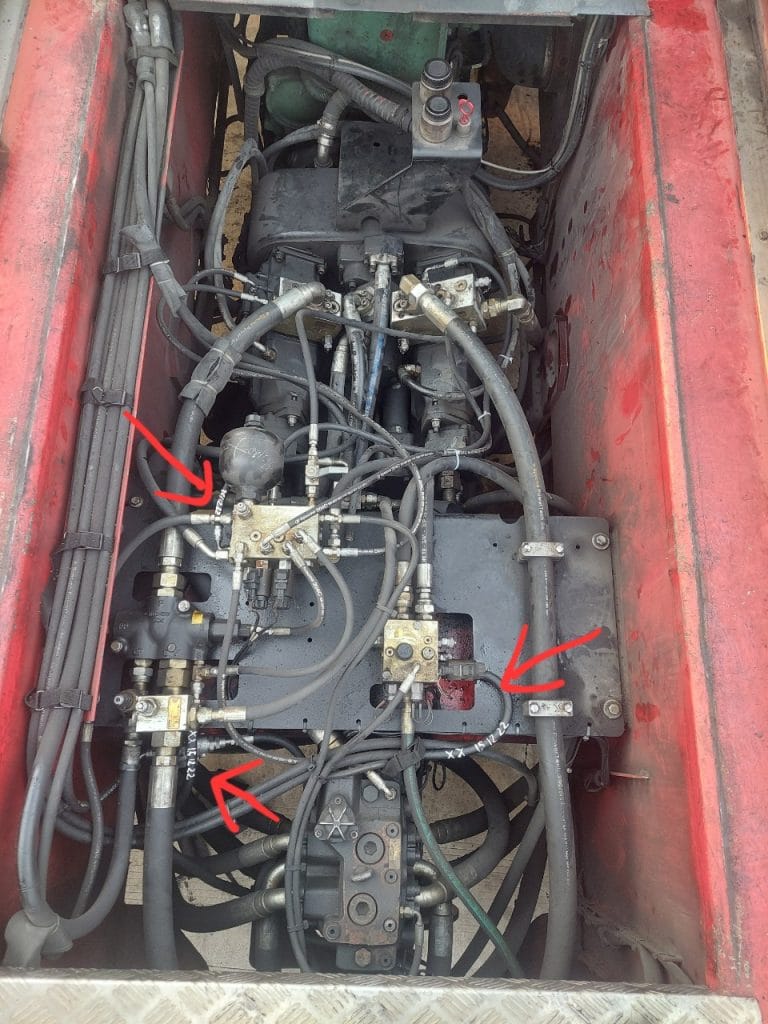
Marine: Steering gears, deck machinery, winches, and hatch covers utilize compact hydraulic systems.
Construction: Hydraulic excavators, loaders, cranes use cylinders and motors for lifting and articulation.
Manufacturing: Hydraulic presses, injection molding machines, and stamping equipment rely on precise force control.
Aerospace: Aircraft use hydraulics for flight control surfaces, landing gear, and braking systems.
Automotive: Braking systems, power steering, and convertible top mechanisms use hydraulic actuation.