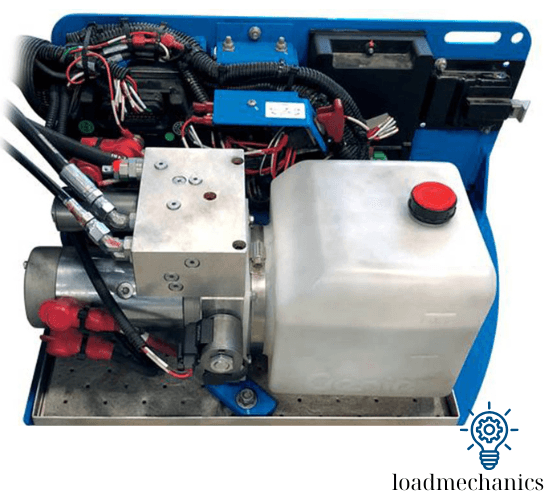
Electric Hydraulic Pump overview
1. Introduction
Electric hydraulic pumps serve as a cornerstone in modern hydraulic system, efficiently converting electrical energy into hydraulic power. Compared to internal combustion-driven alternatives, electric pumps provide superior control, quieter operation, lower emissions, and enhanced integration with automated hydraulic system architectures. They are extensively used across industrial automation, mobile hydraulics, aerospace ground support, precision machine tooling, and heavy construction equipment—making them vital components in both stationary and mobile hydraulic systems.
2. Fundamental Concept and Working Principle
Basic Working Principle of an Electric Hydraulic Pump
An electric hydraulic pump is a system that uses an electric motor (AC or DC) to drive a hydraulic pump, which generates pressurized hydraulic fluid. This fluid is used to power actuators such as hydraulic cylinders or hydraulic motors.
⚙️ Operating Principle:
An electric source powers the electric motor.
The motor’s rotation drives the hydraulic pump.
The pump draws fluid from a reservoir and delivers it under pressure.
Directional control valves guide the fluid to the actuator (e.g., a cylinder).
A relief valve protects the system from overpressure.
Fluid returns to the reservoir, forming a closed-loop circuit.

Detailed Analysis of the Provided Schematic
✅ Component Labels & Functions:
Label Component Description
a Hydraulic Cylinder Double-acting type
b 4/3 Directional Control Valve Controls fluid flow direction, spring-centered
c Relief Valve + Check Valve Overpressure protection and one-way flow
d Hydraulic Pump Driven by the motor
e Hydraulic Reservoir Stores and returns hydraulic oil
f Electric Motor Drives the hydraulic pump
g Power Supply Can supply DC or AC, depending on system type
🔍 Special Note on Component g – Power Supply:
The symbol shows both AC and DC, meaning the system can be powered by:
DC source (e.g., battery) → for mobile applications
AC source (e.g., industrial power) → for stationary systems
Depending on the application, f (motor) may be:
A DC motor – used in portable/mobile units
An AC motor – used in industrial setups
🔄 System Operation Flow:
🔌 1. Startup:
The power unit (g) energizes the motor (f), which rotates the pump (d).
The pump draws fluid from the reservoir (e) and sends it to the control valve (b).
⬆️ 2. Cylinder Extension:
When the solenoid of valve (b) is activated (left coil), fluid is sent to the bottom chamber of the cylinder (a).
The piston extends, performing lifting or pushing work.
⬇️ 3. Cylinder Retraction:
Activating the opposite solenoid sends fluid to the top chamber.
The piston retracts, lowering or pulling back the load.
🛑 4. Neutral/Hold Position:
When no solenoids are activated, center springs return the valve (b) to the neutral (closed center) position.
All ports are blocked or routed to tank, holding the piston in place.
🔁 5. Overpressure Protection:
If system pressure exceeds safe limits, the relief valve (c) opens and fluid is diverted back to the tank (e).
✅ 6. Check Valve Role:
Prevents backflow to protect the pump and stabilize pressure.
📌 Summary:
The diagram illustrates a typical electric-hydraulic actuation circuit.
The power supply (g) can be AC or DC, as indicated by the symbol.
This system is ideal for applications requiring precise linear motion under load, such as:
Lift tables, Hydraulic presses, Vehicle-mounted hydraulic systems
3. Main Components and Functional Architecture of an Electric Hydraulic Pump
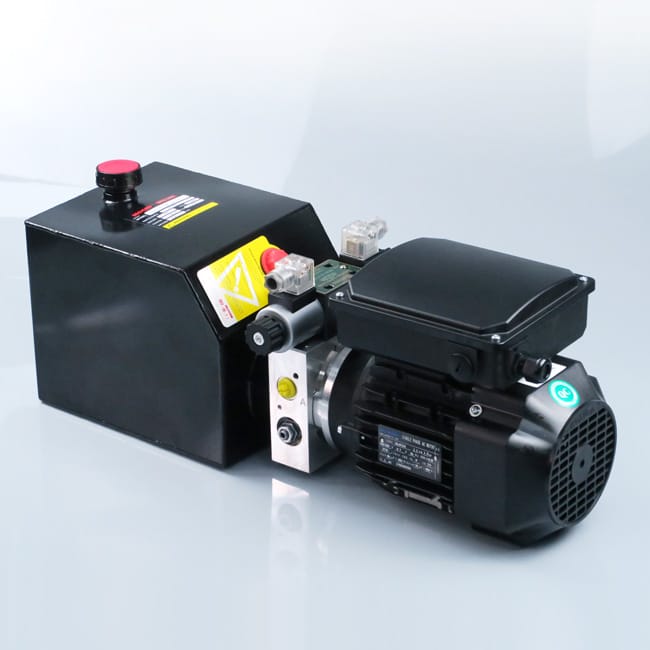
3.1 Electric Motor
- Type: AC (single/three-phase) or DC (brushed/brushless)
- Function: Supplies rotational energy to the pump
- Considerations: Starting torque, duty cycle (continuous vs. intermittent), efficiency, insulation class, thermal protection.
3.2 Hydraulic Pump
- Types:
- Gear Pumps: Robust, inexpensive, fixed displacement
- Vane Pumps: Moderate efficiency, quiet, variable displacement options
- Piston Pumps: High efficiency, capable of high pressure (>350 bar), often variable displacement
- Function: Converts mechanical input into hydraulic energy via fluid displacement
3.3 Hydraulic Reservoir
- Stores hydraulic fluid
- Allows air and contaminants to settle
- Provides thermal mass for heat dissipation
- Includes baffles, suction strainers, and sight gauges
3.4 Pressure Control Valves
- Relief Valve: Protects system from overpressure conditions
- Check Valve: Ensures unidirectional flow
- Pressure Reducing Valve: Maintains pressure in sub-circuits
3.5 Filtration System
- Prevents particulate contamination
- Includes return-line, pressure-line, and suction filters
- Critical for pump longevity and actuator precision
4. Electrical and Control Systems Integration
Modern electric hydraulic pumps are often equipped with:
- Variable Frequency Drives (VFDs): Allow real-time speed control of AC motors to modulate flow and pressure
- Programmable Logic Controllers (PLCs): Enable automation, sequencing, and feedback control loops
- HMI/SCADA Systems: Provide user interfaces and remote monitoring
- Sensors: For pressure, temperature, oil level, and flow rate
This integration makes electric hydraulic pumps ideal for Industry 4.0 and IoT-based fluid power systems.
5. Performance Characteristics
5.1 Flow Rate and Pressure
- Flow rate (Q) is typically specified in L/min or GPM
- Pressure rating depends on the pump type and is typically in the range of 70–700 bar
- Power equation: P=Q×p600(kW)P = \frac{Q \times p}{600} \quad \text{(kW)} P=600Q×p(kW) where QQQ = flow (L/min), ppp = pressure (bar)
5.2 Efficiency
- Volumetric Efficiency (ηᵥ): Ratio of actual flow to theoretical flow
- Mechanical Efficiency (ηₘ): Accounts for mechanical friction losses
- Overall Efficiency: η=ηv×ηm\eta = \etaᵥ \times \etaₘ η=ηv×ηm
High-quality electric hydraulic systems typically exhibit >85% overall efficiency.
5.3 Noise and Vibration
- Electric-driven pumps are quieter than engine-driven systems
- Noise levels vary with pump design — piston pumps tend to be noisier than vane pumps
- Noise mitigation includes acoustic enclosures, vibration isolators, and optimized flow paths
6. Types and Configurations of Electric Hydraulic Pump
6.1 Based on Power Source
- AC Electric Hydraulic Pumps
- Used in fixed installations (220V/380V)
- Continuous duty, high-power systems
- DC Electric Hydraulic Pumps
- Common in mobile systems (12V/24V)
- Used in liftgates, utility trucks, scissor lifts
6.2 Based on Pump Design
- Single-Stage Pumps: Fixed flow and pressure
- Two-Stage Pumps: High-flow low-pressure stage + low-flow high-pressure stage
- Modular Units: Pump, motor, reservoir, and control valves integrated into a compact block
6.3 Portability
- Stationary Pumps: Used in industrial environments
- Portable Pumps: Compact, battery-operated for field service or emergency use
7. Applications
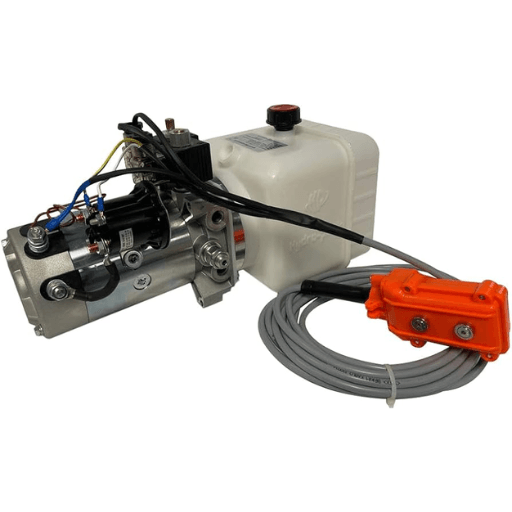
Industry | Application Examples |
---|---|
Manufacturing | Injection molding machines, hydraulic presses, clamping systems |
Automotive | Brake testers, power steering test benches, car lifts |
Construction | Excavator attachment drives, concrete cutter power units |
Aerospace | Ground support equipment (GSE), hydraulic test stands |
Marine | Deck machinery, hatch actuators, steering systems |
Defense | Missile launcher actuation, turret drive systems |
8. Selection Criteria
When selecting an electric hydraulic pump, engineers must evaluate:
- Required flow and pressure
- System voltage and power availability
- Duty cycle and load profile
- Environmental conditions (e.g., IP rating, ambient temperature)
- Mounting configuration and spatial constraints
- Integration compatibility with sensors, PLCs, or motion controllers
9. Advantages Over Engine-Driven and Manual Pumps
- ✔️ Zero Emissions – Ideal for clean environments and enclosed spaces
- ✔️ Automation Ready – Can be seamlessly integrated with CNC and PLC systems
- ✔️ Quiet Operation – Reduced workplace noise and operator fatigue
- ✔️ Precise Control – Real-time feedback, pressure ramping, and closed-loop regulation
- ✔️ Lower Maintenance – No spark plugs, filters, or exhaust system to service
10. Emerging Trends and Future Outlook
- Energy-Efficient Systems: Pumps with smart controllers that operate only on demand (load-sensing control)
- Digital Hydraulics: Integration of electrohydraulic actuators with digital valves for faster, finer control
- Condition Monitoring: Predictive maintenance via built-in sensors and IoT connectivity
- Green Hydraulics: Use of biodegradable hydraulic fluids and energy recovery circuits
Conclusion: Electric Hydraulic Pump
Electric hydraulic pumps are redefining the boundaries of modern fluid power systems by offering precision, adaptability, and energy efficiency. As automation, robotics, and intelligent systems continue to advance, electric-driven hydraulics will remain a central element in high-performance machinery design.
For engineers, understanding the in-depth operation, selection methodology, and integration potential of electric hydraulic pumps is critical in optimizing both legacy and next-generation fluid power systems.